Executive summary
ABC is a mid-size company dealing with the manufacturing and distribution of refrigerators in the Czech Republic. The company has been operating for the past ten years and is well known for good refrigerators. The company is headed by Acquaintance, who is the CEO. The company manufactures LRX refrigerators, a famous brand because they are available everywhere at an affordable cost. The company has more than 12 outlets across the state and more than 20 outlets throughout the country. Over the past six months, the company has suffered a significant loss in product sales. The company has been experiencing many operation problems, including reduced production of the product, inability to meet the orders, production of poor-quality refrigerators, and higher production cost. There arose a need to carry out business process audits to identify the problem and develop the best solution to keep the business productive.
Introduction
Compared to their competitors, the rate of return on investment has greatly reduced due to low sales, poor production, inability to meet orders, and heavy expenditure on the production process. The CEO is stressed since she does not know where the problem is and has asked for external assistance. The business process audits will critically analyze the department of production within the company and suggest possible solutions to the management (Pan et al., 2019). Several data analysis techniques and data gathering methods shall be used.
The goals of the proposal
- Identify the cause of the low level of production
- Investigate the poor-quality nature of the refrigerators produced.
- To identify the reasons for failures in meeting orders
- To identify a long-term solution to the underlying problems.
Determining the process to analyze
Determining the process to analyze is the first step that will be taken to identify the problem within the ABC production department. An as-is process will be selected as it applies to the current process in the business. The benefit of using the as-is process is that it will assist in establishing the benchmarks and measuring the changes made. Two key processes will be analyzed, which are believed to assist in identifying the underlying problem in the production unit. These include sales orders and vendor management (Shad et al., 2019). These two processes are the underlining bottom line of the production processes since they are performed regularly.
The balance issue is a component of efficiency analysis frequently used in corporate practice. It is one of the most useful tools for evaluating and analyzing the prospective options for removing resource shortages, bottlenecks in the manufacturing process, queues, and surpluses of resources and expenditures in connection to the specific market condition (Pan et al., 2019). Nevertheless, it should be kept in mind that the management of the company’s competitiveness strategy may blame the purposeful preservation of excess production resources.
Collection of the business analysis data
This next step will gather information about the previously mentioned processes. Additionally, individuals or the stakeholders involved will be performed as well. These business analysis data reside within the company and outside the business. The processes the employees use in the business in tackling the production shall be documented under this section, the tools used and the steps laid down to be followed by manufacturing these refrigerators. To observe how the process works and what phases are involved, it is important to see someone carry out the production activity from beginning to end.
Methods used for data collection
Both qualitative and quantitative methods will be used in collecting data from the relevant persons. The use of questionnaires, surveys and documents, observations, and interviews, the techniques used for data collection. These techniques will assist in collecting the necessary information that can be used to analyze the possible cause of under production within ABC company. Some techniques will be based on the qualitative data and others will be on quantitative data.
Interviews
Since there is no answer to the cause of the problem the ABC company is experiencing in production, interviewing the employees would be more effective to know about the unknown data. A list of questions will be developed concerning the ABC business’s production state (Shad et al., 2019). For the reliability of the data gathered, the interviews will be done one on one with the employees in the business. The structure of the questions will be open-ended to give the interviewee a chance to explain themselves and respond customized.
Observation
It would also be useful if the observation is done on the production process within the company. The engineers from different companies will do the observation to identify what the ABC company is doing wrong, which affects their productivity. Through observation, the situation’s dynamics generally cannot be measured through interviews and other data collection methods applicable in this case.
Mapping out the production process
After identifying the business process to analyze and collecting the necessary data, there will be a roadmap to executing the audit process within the production department. Through mapping the production process, it will be easy to identify the faults along the process that lead to decreased productivity within the business. The process will be visualized from the start to the finish. The management will be able to visualize every step, like onboarding the employees, the order purchases and approvals, and many more regarding refrigerator production (Aleksandrova et al., 2018). Most businesses fail due to the lack of management overseeing every process in a company. As seen in figure 1 below, the production capacity of particular activities should be calculated based on the stated dependencies. The productivity of the operation, which is the least, determines the total output capacity of the process.
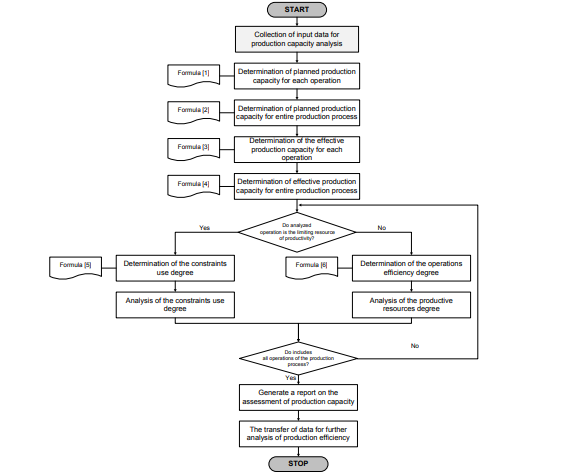
Analyzing and Identifying improvement opportunities
After mapping out the process within the company, one should better understand the areas that need to be improved. Any weaknesses will be identified here, and corrective measures will be suggested. Answers to the following questions will be answered:
- Are any stages taking longer than expected?
- What elements take the most time?
- Do participants have the resources they require?
- Any processes that could be automated or even skipped?
- What are some typical grievances made by the workers?
- Where are human mistakes most likely to happen?
Once these answers are obtained, and by ensuring nothing is missing, the auditing team will solicit feedback from key stakeholders of ABC company. The analysis technique used in this case is the mistake-proofing technique, which looks at each step in the production process flow maps and identifies the kind of mistakes that can be made by human error. The management will be able to pinpoint the bottleneck in refrigerators’ production.
Developing a “To Be” Plan
From the previous analysis, management will be provided with the result that will allow them to modify the process to improve the production technique in the future. In determining productivity capacity, evaluating the production efficiency at the operation level is important (Shad et al., 2019). This method largely depends on the assumed accuracy of the analysis conducted above. Because it is based on matching the available capacity of all resources to expected demand, which consumes the examined production resources, capacity is a critical challenge in terms of production efficiency.
Conclusion
When analyzing the effectiveness of the production process, it should be a goal to boost productivity by making the best use of the instruments at hand in the shortest amount of time (for example, depending on the number of planned changes in production). It should be kept in mind, too, that the increase in production capacity can only be attained when the additional workstations involved are used to their maximum potential. This condition results in reduced levels of investment and a high indication of resource use, but it also lowers production quantities. Due to the absence of comprehensive indicators that may be used to measure productivity, it isn’t easy to provide an accurate and clear assessment of it. Productivity is examined throughout the production process and at the workstation level, specific activity, and overall process. It should be remembered that the greatest number of items that may be produced in a given amount of time is how the efficiency of production resources is defined.
One may review and evaluate various company activities by carrying out a business process analysis. This makes it simpler to see any process bottlenecks adding unnecessary costs to delays. To examine numerous business sector or organization processes, applying (and modifying) the modes and methodologies created while studying one process is a good idea. Users most likely found several processes when they first analyzed the context and made some initial inferences. The moment has come to review them and carry on the sterling work that has begun.
References
Shad, M. K., Lai, F. W., Fatt, C. L., Klemeš, J. J., & Bokhari, A. (2019). Integrating sustainability reporting into enterprise risk management and its relationship with business performance: A conceptual framework. Journal of Cleaner Production, 208, 415-425. Web.
Pan, W., Chen, L., & Zhan, W. (2019). PESTEL analysis of construction productivity enhancement strategies: A case study of three economies. Journal of Management in Engineering, 35(1), 05018013. Web.
Aleksandrova, S. V., Aleksandrov, M. N., & Vasiliev, V. A. (2018). Business continuity management system. In 2018 IEEE International Conference” Quality Management, Transport and Information Security, Information Technologies”(IT&QM&IS) (pp. 14-17). IEEE. Web.