Introduction
Iron is the fourth abundant element on earth, which does not occur in a metallic form in nature. Iron and steel production knowledge spread to North America in the early seventeenth century (Thorne, 2017). The discovery of the Bessemer converter in the nineteenth century led to the modern-day steel age. A combination of iron scrap and a varying amount of carbon form steel. There are numerous steel grades, but carbon, alloy, and stainless steel are the three main types. Carbon steel is the most common steel type in the United States and it contains nearly two percent of carbon. Alloy steel contains four percent of the alloying elements, while stainless steel is produced by combining iron with chromium and nickel to make it resistant to corrosion.
Uses of Steel and Iron
Different grades of steel can be applied in various fields. First, carbon steel is used in the automotive and machinery industry. It is also used in the shipbuilding, construction, and packaging sectors. Alloy steels are used in building machined parts and fabrication of tools. In addition, Thorne (2017) states that steel frames can be used to support some modern buildings. Iron combined with manganese, nickel, tungsten, and chromium form alloy steels. These materials are used to make bicycle chains, rifle barrels and construct bridges. Cast iron containing about three percent carbon is used for manufacturing pipes and pumps.
Main Producers and Consumers of Steel and Iron in the World
The iron and steel industry has undergone an upward growth, which reflects on the state of the global economy. The developed countries, particularly Japan, North America, and Western Europe, accounted for approximately two-thirds of the world’s steel production in the twentieth century. However, the pattern has shifted to the developing nations, in which the iron and steel industry has experienced tremendous changes in the last thirty-five years (Thorne, 2017). In 1980, the world highest steel producers were Japan, USA, Canada, Germany, France, Italy, Brazil, and China. The World Steel Association revealed that in 2014, the total global steel production was 1665mln tonnes, with China being the highest producer (Thorne, 2017). Other top ten leading steel producers worldwide include India, Turkey, Russia, and South Korea.
All forms of iron, including cast iron and steel, are the most used construction materials globally. The mineral competes with wood, cement, and new constructional materials, such as ceramics. The engineering sector has consistently used ferrous materials for construction for many years. Global steel consumption is continuously increasing, with the average growth rate in 2014 being three percent (Thorne, 2017). Developed countries have a lower consumption growth rate than developing countries by about two percent.
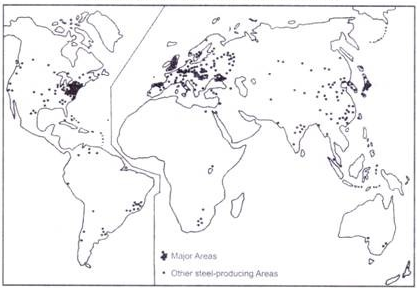
Types of Mineral Deposits
Iron ores are the rocks from which experts extract metallic iron. The ores have plenty of iron oxides and are of varying colors, including dark grey, rusty red, yellow or deep purple. Iron ores are the raw materials used in the manufacture of pig iron, one of the resources used to make steel. The four major iron ore deposits are magnetite, hematite, limonite, and siderite. Iron ores can be categorized into two; high grade and low-grade ores. Hematite and limonite are the two high-grade iron ores that produce the highest quantities of iron. These ores can be fed directly into the blast furnaces to produce iron. Large deposits of massive hematite ore are formed by passing fluids that eliminate the non-iron bearing minerals and enrich the ore with iron minerals. Rocks rich in siderite and magnetite minerals provide low-grade ores. These elements may be beneficiated through wet-magnetic separation to produce iron.
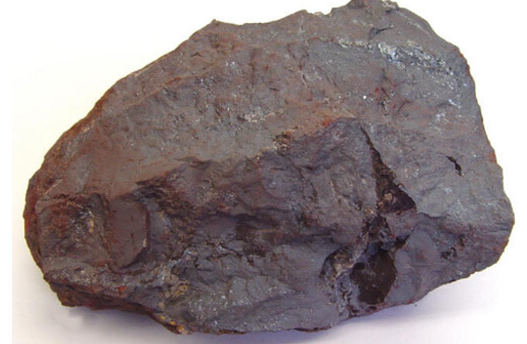
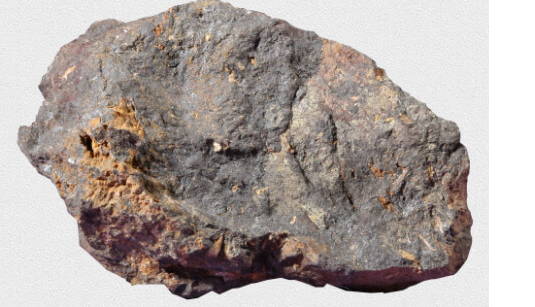
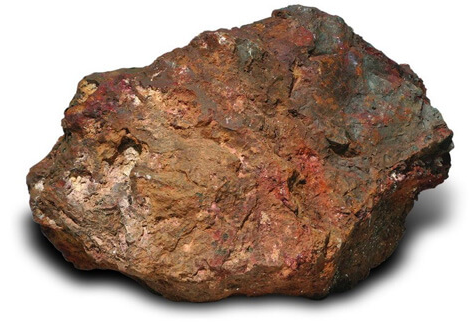
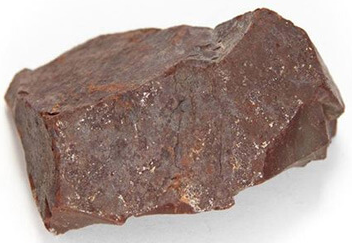
Mining and Refining Process
Pig iron is a raw material used in the manufacture of steel. The three main steelmaking processes remove a specific carbon amount and replace it with a different element. One procedure, referred to as a secondary steelmaking process, involves using an electric furnace, which contains a water-cooled refractory lined vessel with a retractable roof. The furnace uses electric arcs to melt down the mineral, and oxygen is blown into the scrap to combust the steel. The slag formed minimizes excessive heat loss and erosion of the refractory lining. Electric furnaces are more controllable; therefore, they manufacture high-specification carbon and tool steels. The steel refining process purifies the impure metal but maintains its chemical composition. Professionals can use pyrometallurgical or hydrometallurgical methods to refine steel.
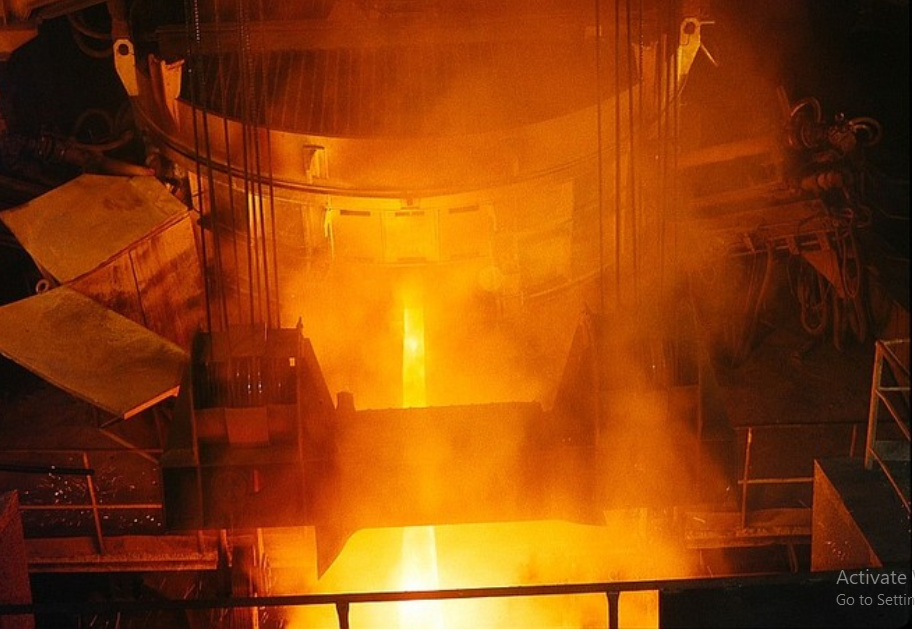
The iron-making process releases iron in a chemically-combined state with oxygen. The blast furnace is an effective process in producing iron. The blast furnace exchanges heat and oxygen and the combustion gas loses heat when rising, leaving the furnace at around 200 degrees Celsius heat. The iron oxides descending on the furnace then convert to metallic iron due to the high furnace temperatures.
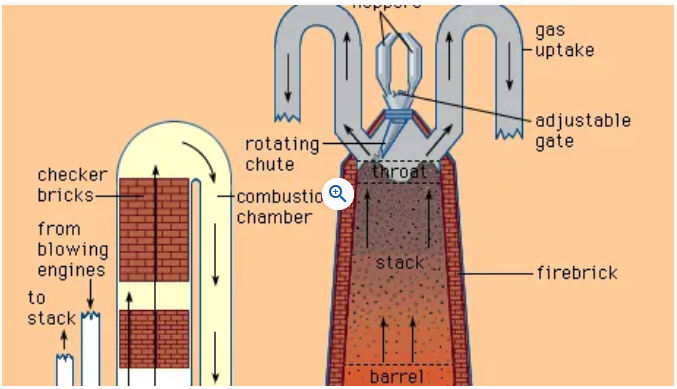
Environmental Problems and Potential Solutions
The extraction and production process of minerals causes environmental problems. Specifically, the iron and steel-making industry contribute the biggest environmental impact (Olmez et al., 2016). The steel-making procedure has numerous consequences on the environment, including gas emissions like sulfur oxides, nitrogen oxides, and carbon dioxides that contribute to global warming and climate change. Additionally, integrated steel mills impact the surroundings through coking and iron-making operations that cause air pollution. Furthermore, many iron and steel industries operate large underground mines that emit gases into the air. Surface operations like rock sizing, breaking and crushing release a lot of dust, and the ore mining process leads to noise pollution.
The potential solution to noise pollution is using topographical features that minimize the effects of sound in residential areas. Siting industrial developments away from mining and quarrying areas will mitigate the effects of increased dust in the air. Additionally, iron and steel production companies should pay close attention to their working practices to effectively control the environmental impacts of their operations. They should employ well-designed engineering pieces of equipment in their operations and observe strict dust containment methods.
Current Economic Outlook
The Iron and Steel Market Research Report 2022 provides accurate figures for the market status of iron and steel manufacturers. The experts considered 2021 as the base year and 2022-2026 as the forecast period for the study (OECD, 2020).. The World Steel Association, October Outlook Report, indicated that the world steel demand in 2022 increased by 2.2% from 1855.4 Mt to 1896.4 Mt (OECD, 2020). Based on this summary, the global steel demand increased faster than expected in 2021, and the trend is anticipated to continue.
Conclusion
To conclude, the iron and steel sector forms the base for developing the defense, energy, construction, and transportation industries. Furthermore, the industry closely relates to the light and chemical sectors, showing the industry’s significance in promoting national economic growth. The metal’s versatility and strength made it a building block of the Industrial Revolution. The mineral’s production and consumption regions are spread worldwide in Japan, China, Turkey, the USA, and Brazil. The iron and steel industry is expected to experience an upward trend in the coming years.
References
Chand, S. (n.d.). Distribution of iron and steel industry in major countries of the world (with maps). Web.
(JXSC, 2018). Types of iron ore. Web.
Organization for Economic Co-operation and Development. (OECD, 2020). Steel market developments: Q4 2020. Web.
Olmez, G., Dilek, F., Karanfil, T., & Yetis, U. (2016). The environmental impacts of iron and steel industry: A life cycle assessment study. Journal of Cleaner Production, 130, 195-201. Web.
Thorne, R. (Ed.). (2017). Structural Iron and Steel, 1850–1900. Routledge. Web.
Walker, D. (2022). Iron processing. Web.
Wente, E. (2021). Steel. Web.